2025 Автор: Howard Calhoun | [email protected]. Последно модифициран: 2025-06-01 07:13
Устройствата за отложено коксиране са най-разпространеното хардуерно решение за рафиниране на тежък нефт. Устройството им включва 2 основни модула - реактор, където суровината се нагрява и коксува, и механична обработка. Проектирането на инсталациите се извършва на етапи и включва изчисляване и избор на технологично оборудване, определяне на технически и икономически показатели.
Дестинация
Технологичният процес на коксуване е един от начините за рафиниране на нефт. Основната му цел е получаването на едри бучки нефтен кокс. Има 3 метода на коксиране, използвани в индустрията:
- Периодично, на кубчета. Суровината се зарежда в хоризонтален апарат, загрява се с камина под нея, след което се калцинира за 2-3 часа. След това пещта се охлажда и готовият продукт се разтоварва. Този метод е най-простият и най-малко продуктивен.
- Непрекъснато. Този метод все още е на етап индустриално развитие.
- Полунепрекъснато, получено в моментанай-разпространеният.
Ултра-отложените коксови агрегати са най-новият тип технологично оборудване. При тях суровината се загрява предварително в пещ, след което се прехвърля в неотопляеми реакционни камери, които имат топлоизолационен слой за поддържане на необходимата температура. Броят и размерът на реакторите, мощността на пещите влияят върху работата на цялата инсталация.
Експлоатацията на първия DCU в Русия започва през 1965 г. в Уфанефтехим. Забавеният кокс на завода все още работи днес. След реконструкция през 2007 г. производителността му е около 700-750 хил. тона/година по отношение на масата на преработените суровини.
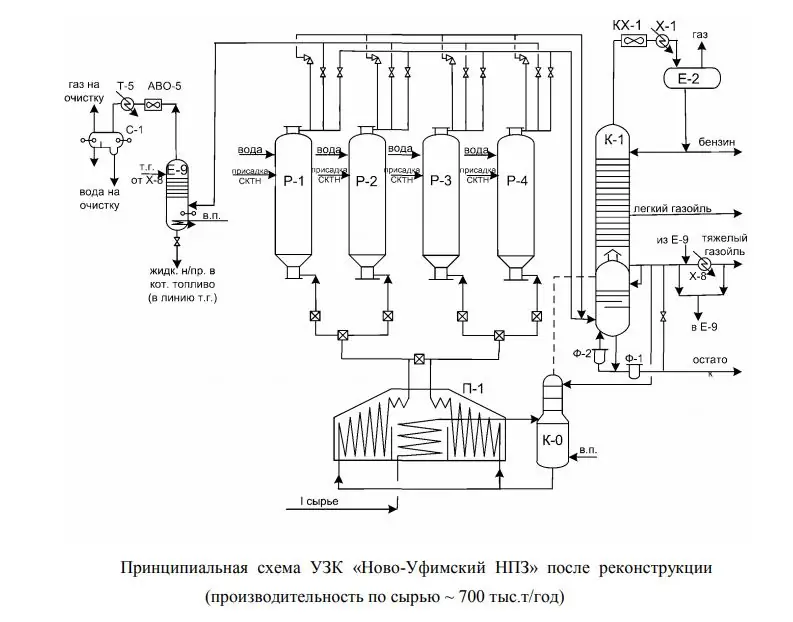
Крайни продукти
Следните вещества се получават при ултразвуково изследване, с изключение на кокс:
- коксуващи се газове (използвани като технологично гориво или преработени за получаване на фракция пропан-бутан);
- бензин;
- коксови дестилати (гориво, суровина за крекинг).
При домашни ултразвукови машини за тестване добивът на кокс е 20-30% тегловни. Този показател зависи преди всичко от качеството на суровините. Металургичната индустрия изпитва най-голяма нужда от този продукт (производство на аноди и електроди, алуминий, абразиви, карбиди, въглерод-графитни материали, феросплави). В допълнение към първия Уфа DCU, в Русия са построени и други агрегати за забавен кокс: в Омската рафинерия, Новокуйбишевска рафинерия, LLC ЛУКОЙЛ-Волгограднефтепереработка, ЛУКОЙЛ-Пермнефтеоргсинтез, ЛУКОЙЛ-Permnefteorgsintez, в Angarsk Petrochemical Company, NOVOIL OJSC (Уфа), TANECO PJSC (Нижнекамск).
Суровини
Хранителните материали за коксуване са разделени на 2 групи: продукти на първична и вторична преработка. Следните вещества се използват като суровини в агрегатите за забавено коксуване:
- гориво;
- половин катран;
- tar;
- катран с въглищен катран;
- асфалт и други промишлени петролни продукти;
- течни остатъци от въглища;
- тежка пиролиза и шистов катран;
- остатъци от термично крекинг;
- нефтен битум и тежки масла.
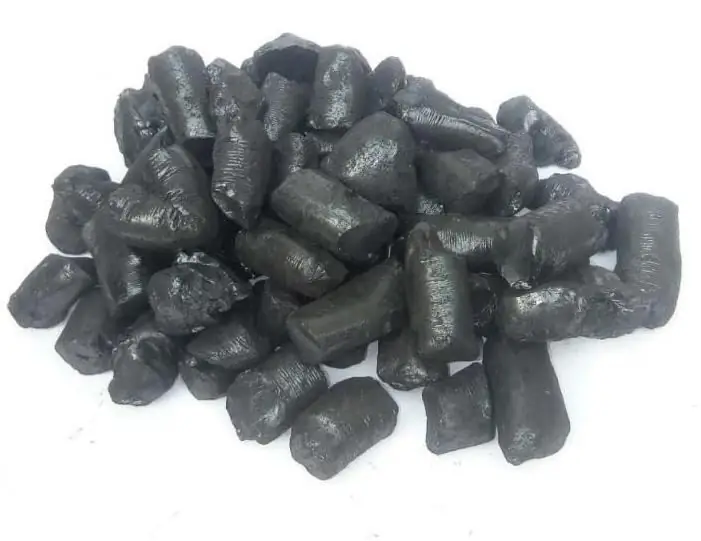
Силно ароматизираните маслени остатъци са най-разпространената суровина в момента.
Влияние върху технологичните параметри
Следните параметри на коксовата инсталация зависят от свойствата на фуражните материали:
- ефективност на реакционната камера;
- качество на получените продукти;
- изход за кокс;
- условия за процеса.
Най-важните параметри на суровината са:
- Коксуване, в зависимост от съдържанието на асфалто-смолистите вещества. Стойността на коксуване трябва да бъде в диапазона от 10-20%. При по-малка стойност добивът на кокс намалява, а при по-голям се натрупват отлагания вътре в намотките в пещите. Капацитетът на коксуване се определя от масата на твърдия остатък в тигела след нагряване на пробата от нефтопродукта в него.
- Плътност.
- Химичен състав. Отвредни примеси, които имат най-голямо влияние върху качеството на кокса, отделят сяра (тя трябва да бъде не повече от 1,5% от теглото). В зависимост от предназначението на кокса в технологичния процес е за предпочитане да се използват различни видове суровини. Така че, за да се получи влакнеста структура на крайния продукт, се използват материали с парафинова основа.
Добивът на кокс е пропорционален на плътността на фуража и съдържанието на асфалтени.
Етапи на кокс
Технологичният процес в агрегатите за забавено коксуване е дълъг и непрекъснат, от доставката на суровини до разтоварването на готовия продукт. Обикновено се разделя на 3 етапа:
- Реакции на разлагане, образуване на дестилатни фракции, междинни продукти, кондензация.
- Значително намаляване на съдържанието на ненаситени въглеводороди в газовете, повишаване на молекулното тегло на остатъчните компоненти, реакции на циклизиране.
- Увеличаване на съдържанието на асфалтени в остатъка до 26%, намаляване на количеството смоли и масла. Преобразувайте течния остатък в твърд кокс.
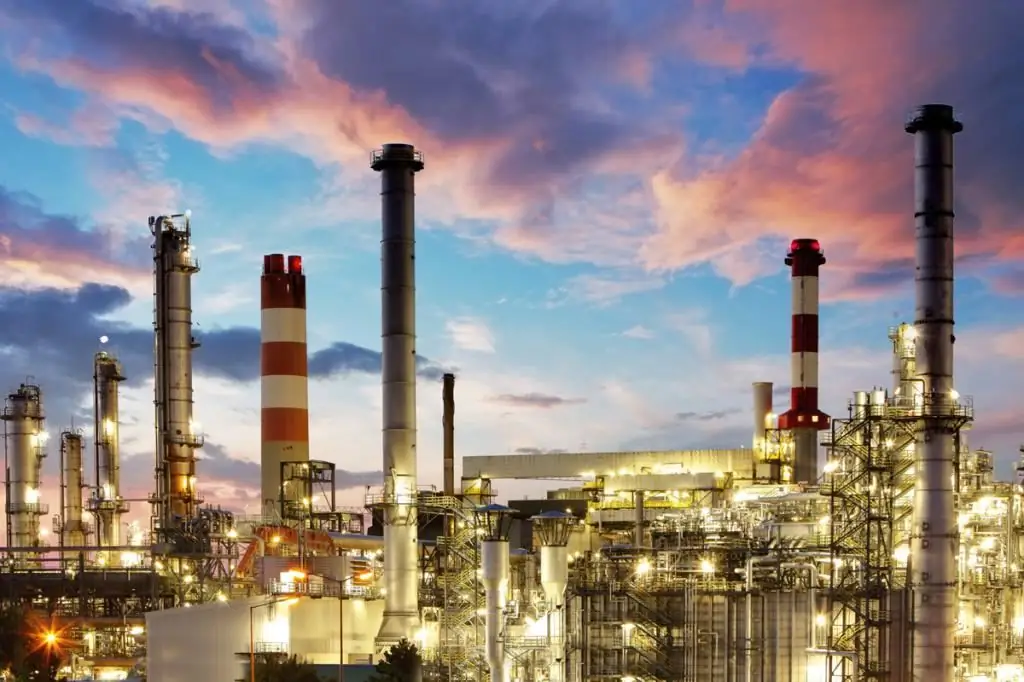
Класификация
Има 2 основни типа агрегати за отложено коксиране според тяхното разположение: едноблокови и двойни блокове.
Сред двублоковите инсталации има 4 вида, които се характеризират със следните конструктивни и технологични характеристики:
- Вътрешен диаметър на коксовите камери - 4,6 м. Пещи за нагряване на палатка, четири камери, работещи по двойки. Керосинът и газьолът, получени по време на процеса на коксуване, се използват за нагряване.
- Кока-колакамери Ø 5,5 м. Изходна суровина - директни горива с внасяне на силно ароматни въглеводороди, които повишават добива на качествен продукт.
- Реактори от легирана стомана Ø 5,5 m, височина 27,6 m, тръбни пещи с факел за обемно полагане, горни вентили с увеличено напречно сечение, радиоактивни нивомери, които позволяват регистриране на местоположението на разделяне на фазата на кокс-пяна. Последната иновация помага за по-доброто използване на полезния обем на реактора. Доставка на турбулатори с почистващи добавки за намаляване на коксуването на серпенти, охладен газьол в главни тръби.
- Реакционни камери Ø 7 м, височина 29,3 м. Аксиално подаване на суровина в реакторите, хидравлична система за разтоварване на кокс с дистанционно управление, електрически кранове, складове с подов тип склад.
Приложно оборудване
Оборудването, което е оборудвано с инсталации от този тип, се разделя на следните групи в зависимост от предназначението:
- Технологични, пряко участващи в процеса на коксуване (пещи, колонно оборудване, топлообменници, реакторни камери, кубове, хладилници, помпи, тръбопроводи, инструменти, кранове и други спирателни и превключващи вентили).
- Отпадъчни води - събиране и пречистване на водата за връщане към работния цикъл (операции по охлаждане и извличане на кокс).
- Оборудване за разтоварване на кокс от камери (кубове). В съвременните механизирани инсталации може да бъде от механичен и хидравличен тип (сапани, лебедки, гребени, фрези, пръти, кули, гумени втулки).
- Устройства за транспортиране и обработка на готовия продукт (приемни улеи и рампи, кранове, транспортьори, хранилки, трошачки, складове).
- Машини и съоръжения за механизация на работата.
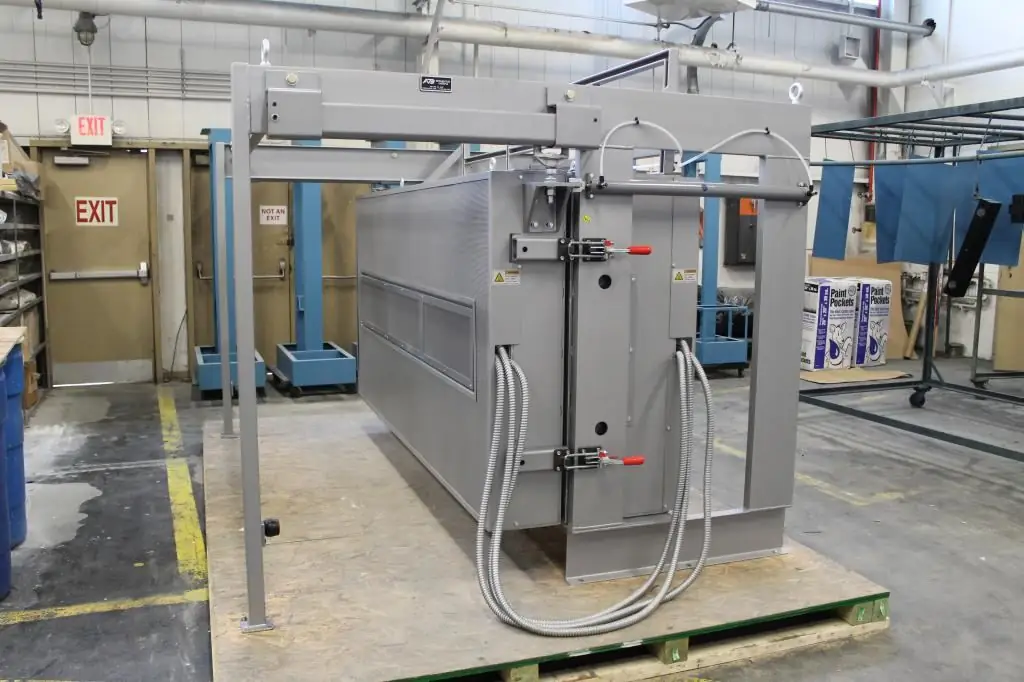
При проектирането на инсталации за забавено коксуване е необходимо внимателно да се обмисли дизайна на реакционните камери и пещи, тъй като продължителността на работния цикъл зависи от надеждността на тяхната работа.
Параметри на процеса
Основните параметри на технологията за коксуване са:
- Коефициент на рециркулация, дефиниран като съотношението на общото натоварване на реакционните намотки на пещите към натоварването на цялото предприятие по отношение на суровините. С увеличаване на стойността му добивът на висококачествен кокс, газ и бензин се увеличава, но количеството тежък газьол намалява.
- Налягане в реакционната камера. Намаляването му води до увеличаване на добива на газьол, намаляване на добива на кокс и газ и увеличаване на образуването на пяна.
- Температура на процеса. Колкото по-голям е той, толкова по-високо е качеството на кокса по отношение на количеството летливи вещества, неговата сила и плътност. Максималната стойност е ограничена от риска от коксуване на пещта и тръбопроводите, което намалява издръжливостта на намотките. Всеки вид суровина има своя собствена оптимална температура.
Изграждането на агрегати за забавено коксуване е свързано с високи капиталови разходи. Ето защо най-често се извършва реконструкция на вече функциониращ комплекс от оборудване. Това се постига чрез намаляване на цикълакоксуване, въвеждане на нови реакционни камери или намаляване на съотношението на рециркулация.
Принцип на действие
Агрегатите за отложено коксиране се състоят от една или повече сдвоени групи камери, в които едната камера работи на етапа на производство на кокс, а другата при разтоварване или в междинно състояние. Процесът на разлагане на изходния материал започва в тръбна пещ, където се нагрява до 470-510 °C. След това суровината влиза в неотопляеми камери, където се коксува дълбоко поради топлината, която идва заедно с него.
Газообразните и течните въглеводороди се изхвърлят за фракционно разделяне в дестилационна колона. Коксът влиза в отдела за механична обработка, където се разтоварва, сортира и транспортира. В слоя на готовия продукт се пробива кладенец и в него се поставя хидравличен резец. Неговите дюзи работят под налягане до 20 MPa. Парчета от отделения кокс падат върху дренажна платформа, където водата се оттича. След това продуктът се натрошава на по-малки парчета и се разделя на фракции. След това коксът се премества в склада.
Принципната диаграма на ултразвука е показана на фигурата по-долу.
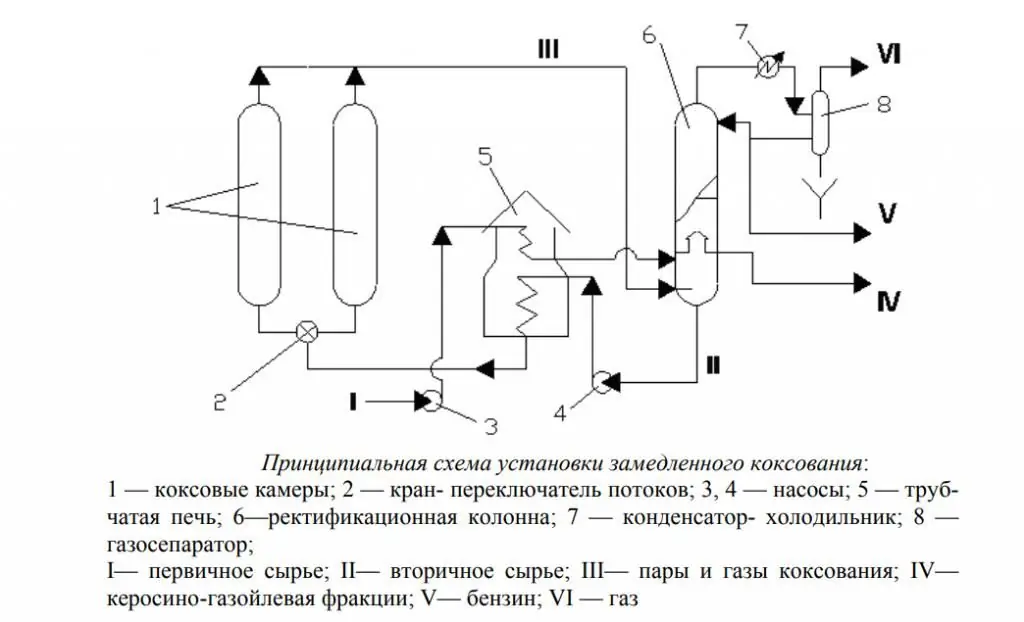
Коксови камери
Камерите са реактор, който е в основата на цялата инсталация. Цикълът на работа на камерата обикновено е 48 часа, но през последните години са проектирани ултразвукови устройства, работещи в 18- и 36-часов режим.
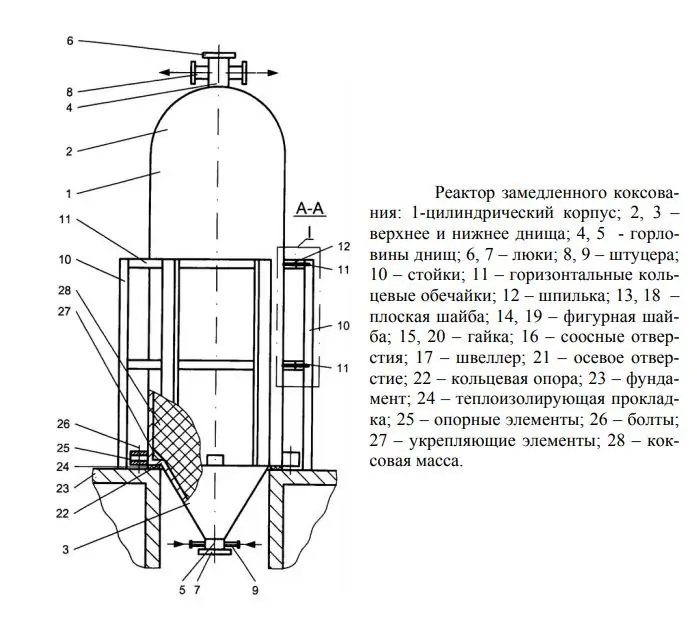
Един цикъл на работа на реактора се състои от следните операции:
- зареждане на суровини, процес на коксиране (1 ден);
- изключване (1/2 час);
- хидротермална обработка (2,5 часа);
- водно охлаждане на продукта, отстраняване на водата (4 часа);
- разтоварване на продукта (5 часа);
- запечатване на шахти, изпитване под налягане с гореща пара (2 часа);
- нагряване с маслени пари, преминаване към работен цикъл (3 часа).
Дизайн
Проектът за отложено коксуване се разработва в следния ред:
- определяне на необходимата производителност, t/година;
- анализ на базата на ресурсите;
- изготвяне на теоретичен материален баланс на процеса на коксиране за различни видове суровини;
- определяне на основните материални потоци;
- разработване на концепцията за инсталация;
- обосновка за размера и броя на реакторите;
- определяне на продължителността на пълнене на една камера с кокс и нейното хидравлично изчисление, съставяне на график за работа на реактора;
- изчисления на температурното натоварване на камерата;
- изчисление на конвективни и радиационни камери;
- разработване на оформлението на производствената линия;
- технологични изчисления на друго основно оборудване (дестилационна колона, пещи, хладилници и др.);
- разработване на система за наблюдение и контрол, избор на инструменти за автоматизация;
- описание на схемите за аварийна защита;
- разработване на екологични аспекти и мерки за безопасност;
- определяне на икономически показатели (капиталови разходи, брой обслужващ персонал, заплати,производствени разходи за суровини и спомагателни материали, годишен икономически ефект, себестойност на продукта).
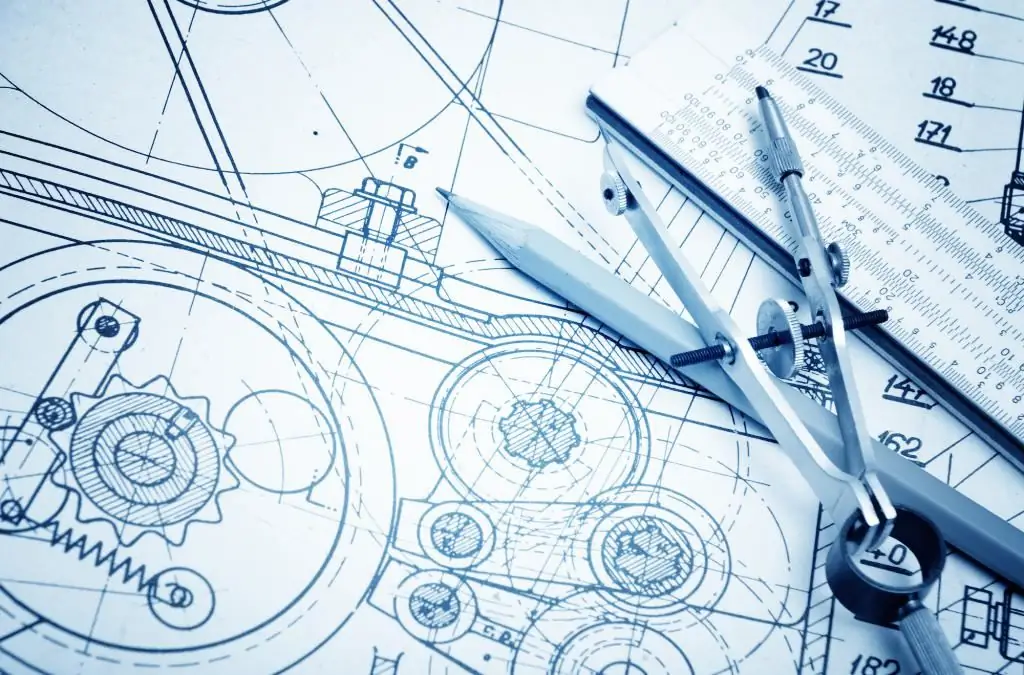
Изчисляването на капацитета на блока за отложено коксиране на годишна база се извършва по формулата:
N=P x t, където P е капацитетът на инсталацията, t/ден;
t е броят на работните дни в годината.
Продуктът във физическо изражение в зависимост от основата и опциите за дизайн се определя въз основа на материалния баланс на инсталацията.
Препоръчано:
Електрически локомотив 2ES6: история на създаването, описание със снимка, основни характеристики, принцип на работа, характеристики на работа и ремонт
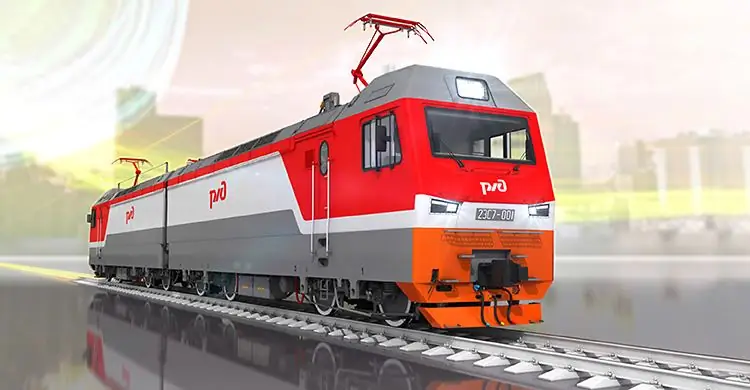
Днес комуникацията между различните градове, превозът на пътници, доставката на стоки се осъществява по различни начини. Един от тези пътища беше железопътната линия. Електрически локомотив 2ES6 е един от видовете транспорт, които в момента се използват активно
Машина за диамантено пробиване: видове, устройство, принцип на работа и условия на работа
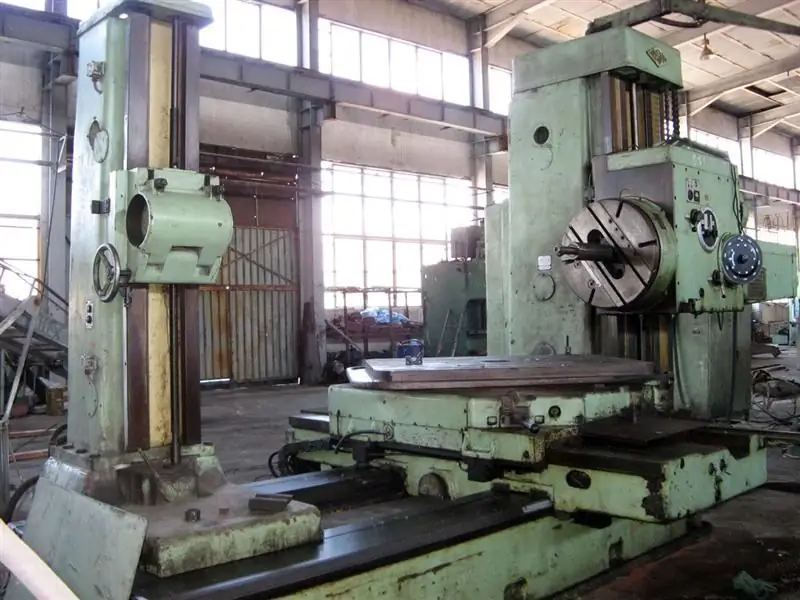
Комбинацията от сложна конфигурация на посоката на рязане и твърдотелно работно оборудване позволява на диамантеното пробиващо оборудване да извършва изключително деликатни и критични металообработващи операции. На такива агрегати се поверяват операциите по създаване на оформени повърхности, корекция на дупки, обвързване на краищата и т.н. В същото време диамантената пробивна машина е универсална по отношение на възможностите за приложение в различни области. Използва се не само в специализирани производства, но и в частни работилници
Какво е технологичен проект? Разработване на технологичен проект. Пример за технологичен проект
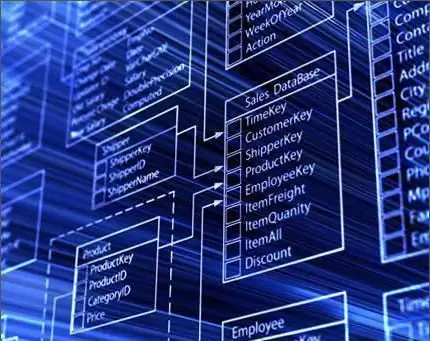
Като част от статията ще разберем какво е технологичен проект, а също така ще изработим проблемите на неговото развитие
Разрешение за работа за работа в електрически инсталации. Правила за работа в електрически инсталации. Разрешително за работа
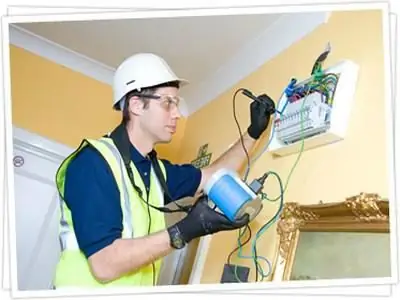
От август 2014 г. влиза в сила Закон № 328n. В съответствие с него се въвежда нова редакция на "Правила за охрана на труда при експлоатация на електрически инсталации"
Трифазна мрежа: изчисляване на мощността, схема на свързване
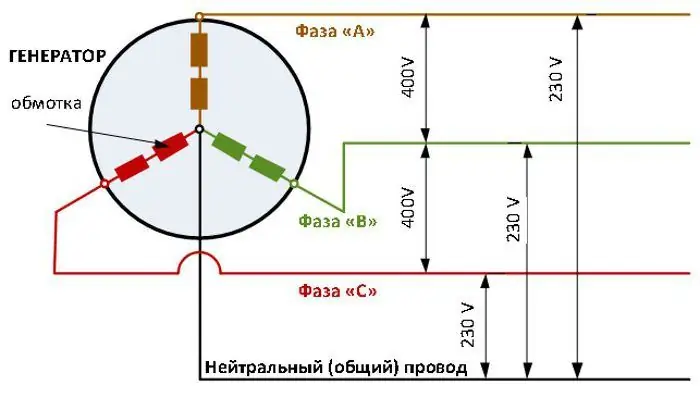
Когато е правилно проектирана и поддържана, трифазната мрежа е идеална за частен дом. Тя ви позволява да разпределите равномерно натоварването между фазите и да свържете допълнителни консуматори на енергия, ако секцията на окабеляването позволява