2025 Автор: Howard Calhoun | [email protected]. Последно модифициран: 2025-01-24 13:12
Метрологията е наука за измерванията, средствата и методите за осигуряване на тяхното единство, както и начините за постигане на необходимата точност. Негов предмет е подборът на количествена информация за параметрите на обектите с дадена надеждност и точност. Нормативната рамка за метрологията са стандарти. В тази статия ще разгледаме системата от толеранси и кацания, която е подраздел на тази наука.
Концепцията за взаимозаменяемост на части
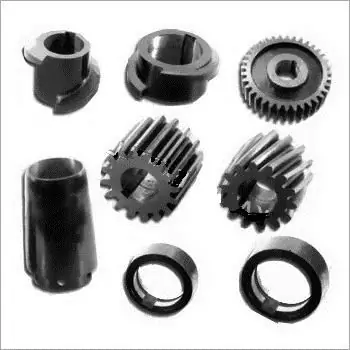
В съвременните фабрики трактори, коли, металорежещи машини и други машини се произвеждат не на единици или десетки, а на стотици и дори хиляди. При такива обеми на производство е много важно всяка произведена част или възел да пасне точно на мястото си по време на монтажа без допълнителни ключарски настройки. В крайна сметка такива операции са доста трудоемки, скъпи и отнемат много време, което е неприемливо при масово производство. Също толкова важно е частите, влизащи в монтажа, да позволяват смяна.за други общи цели с тях, без да нарушават функционирането на целия готов блок. Такава взаимозаменяемост на части, възли и механизми се нарича унификация. Това е много важен момент в машиностроенето, той ви позволява да спестите не само разходите за проектиране и производство на части, но и време за производство, освен това опростява ремонта на продукта в резултат на неговата работа. Взаимозаменяемостта е свойството на компонентите и механизмите да заемат местата си в продуктите без предварителен избор и да изпълняват основните си функции в съответствие със спецификациите.
Свързани части
Две части, фиксирани или подвижно свързани една с друга, се наричат чифтосване. И стойността, с която се извършва тази артикулация, обикновено се нарича размер на чифтосване. Пример е диаметърът на отвора в макарата и съответния диаметър на вала. Стойността, с която връзката не се осъществява, обикновено се нарича свободен размер. Например външният диаметър на макарата. За да се осигури взаимозаменяемост, съвпадащите размери на частите трябва винаги да са точни. Тази обработка обаче е много сложна и често непрактична. Следователно в технологията се използва метод за получаване на взаимозаменяеми части при работа с така наречената приблизителна точност. Той се крие във факта, че за различни работни условия, възли и части задават допустимите отклонения на техните размери, при които е възможно безупречното функциониране на тези части в уреда. Такива компенсации, изчислени за различни работни условия, се изграждат в даденаопределена схема, името му е "единна система от толеранси и кацания".
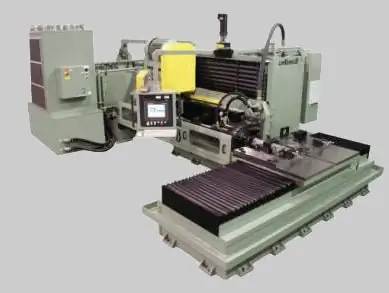
Концепцията за допустимите отклонения. Количествени характеристики
Изчислените данни за частта, предоставена на чертежа, от която се отчитат отклоненията, обикновено се наричат номинален размер. Обикновено тази стойност се изразява в цели милиметри. Размерът на частта, който реално се получава при обработката, се нарича действителен размер. Стойностите, между които този параметър се колебае, обикновено се наричат граница. От тях максималният параметър е най-голямата граница за размер, а минималният параметър е най-малкият. Отклоненията са разликата между номиналната и граничната стойност на дадена част. В чертежите този параметър обикновено е посочен в цифров вид с номинален размер (горната стойност е посочена по-горе, а долната стойност отдолу).
Пример за вписване
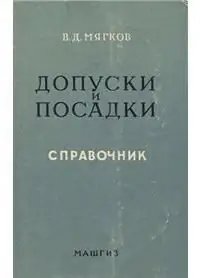
Ако чертежа показва стойността 40+0, 15-0, 1, тогава това означава, че номиналният размер на част е 40 мм, най-голямата граница е +0,15, най-малката е -0,1. Разликата между номиналната и максималната гранична стойност се нарича горно отклонение, а между минималното - долно. Оттук действителните стойности се определят лесно. От този пример следва, че най-голямата гранична стойност ще бъде равна на 40+0, 15=40,15 mm, а най-малката: 40-0, 1=39,9 mm. Разликата между най-малкия и най-големия гранични размери се нарича толеранс. Изчислено, както следва: 40, 15-39, 9=0,25 мм.
Пропуски и плътност
Нека помислимконкретен пример, при който допуските и приляганията са ключови. Да предположим, че имаме нужда от част с отвор 40+0, 1, за да се побере на вал с размери 40-0, 1 -0, 2. От условието може да се види, че диаметърът за всички опции ще бъде по-малък от отвора, което означава, че при такава връзка задължително ще се появи празнина. Такова кацане обикновено се нарича подвижно, тъй като валът ще се върти свободно в отвора. Ако размерът на частта е 40+0, 2+0, 15, тогава при всяко условие тя ще бъде по-голяма от диаметъра на отвора. В този случай валът трябва да бъде натиснат и ще има смущения във връзката.
Заключения
Въз основа на горните примери могат да се направят следните изводи:
- Разликата е разликата между действителните размери на вала и отвора, когато последният е по-голям от първия. С тази връзка частите имат свободно въртене.
- Предварително натоварване обикновено се нарича разликата между действителните размери на отвора и вала, когато последният е по-голям от първия. С тази връзка частите се притискат.
Поставя и класове по точност
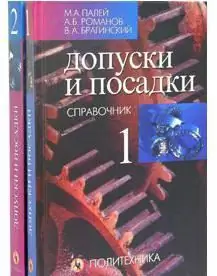
Приземленията обикновено се делят на фиксирани (горещи, натискащи, лесно натискане, глухи, стегнати, плътни, напрегнати) и подвижни (плъзгащи се, бягащи, движение, лесно бягане, широко бягане). В машиностроенето и приборостроенето има определени правила, които регулират допуските и кацанията. GOST предвижда определени класове на точност при производството на възли, използващи определени отклонения на размерите. От практикатаИзвестно е, че детайлите на пътните и селскостопанските машини без вреда за тяхното функциониране могат да бъдат произведени с по-малка точност, отколкото за стругове, измервателни уреди и автомобили. В тази връзка толерансите и пасванията в машиностроенето имат десет различни класа на точност. Най-точните от тях са първите пет: 1, 2, 2а, 3, 3а; следващите две се отнасят за средна точност: 4 и 5; и последните три към грубо: 7, 8 и 9.
За да разберете до какъв клас на точност трябва да бъде изработена детайла, на чертежа, до буквата, указваща прилягането, поставете число, указващо този параметър. Например, маркирането C4 означава, че типът е плъзгащ се, клас 4; X3 - ходов тип, клас 3-ти. За всички кацания от втори клас не се поставя цифрово обозначение, тъй като е най-често срещаното. Можете да получите подробна информация за този параметър от двутомния справочник "Допуски и прилягания" (Мягков В. Д., издание 1982 г.).
Система за вал и дупки
Толерантността и приляганията обикновено се разглеждат като две системи: дупки и валове. Първият от тях се характеризира с факта, че в него всички типове с еднаква степен на точност и клас се отнасят до един и същ номинален диаметър. Отворите имат постоянни стойности на граничните отклонения. Разнообразие от кацания в такава система се получава в резултат на промяна на максималното отклонение на вала.
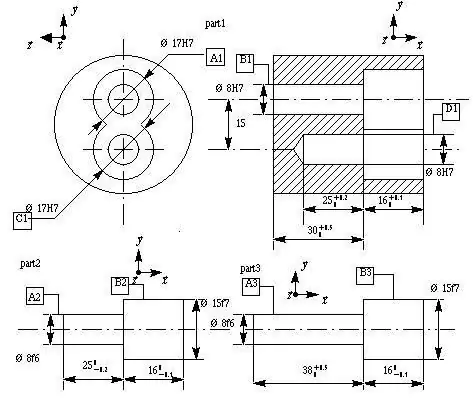
Вторият от тях се характеризира с това, че всички типове с еднаква степен на точност и клас се отнасят за един и същ номинален диаметър. Валът има постоянни гранични стойностиотклонения. В резултат на промяна на стойностите на максималните отклонения на дупките се извършват различни кацания. В чертежите на системата от отвори е обичайно да се обозначава буквата A, а валът - буквата B. Близо до буквата е поставен знакът за класа на точност.
Примери за символи
Ако на чертежа е посочено "30A3", това означава, че въпросната част трябва да бъде обработена със система от отвори от трети клас на точност, ако е посочено "30A", това означава използване на същата система, но вторият клас. Ако толерансът и прилягането са направени според принципа на вала, тогава необходимият тип се посочва при номиналния размер. Например, част с обозначението "30B3" съответства на обработката на валовата система от трети клас на точност.
В своята книга M. A. Paley („Допуски и прилягания“) обяснява, че в машиностроенето принципът на отвора се използва по-често от вал. Това се дължи на факта, че изисква по-малко оборудване и инструменти. Например, за да се обработи отвор с даден номинален диаметър според тази система, е необходим само един райбер за всички площадки от този клас и една ограничителна тапа за промяна на диаметъра. При система с валове са необходими отделен райбер и отделен щепсел, за да се гарантира, че всяко пасва в един и същ клас.
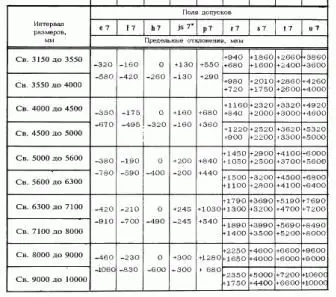
Допуски и прилягания: таблица на отклоненията
За определяне и избор на класове на точност е обичайно да се използва специална справочна литература. Така че толерансите и пасванията (в тази статия е дадена таблица с пример) като правило са много малки стойности. Заза да не се пишат допълнителни нули, в литературата те са обозначени в микрони (хилядни от милиметъра). Един микрон съответства на 0,001 мм. Обикновено номиналните диаметри са посочени в първата колона на такава таблица, а отклоненията на отвора са посочени във втората. Останалите графики дават различни размери на кацанията със съответните им отклонения. Знакът плюс до такава стойност показва, че трябва да се добави към номиналния размер, знакът минус показва, че трябва да бъде изваден.
Нишки
Толерантността и напасванията на резбовите връзки трябва да отчитат факта, че резбите се съединяват само отстрани на профила, само паронепропускливите видове могат да бъдат изключение. Следователно основният параметър, който определя естеството на отклоненията, е средният диаметър. Толерансът и приляганията за външния и вътрешния диаметър са зададени така, че напълно да се елиминира възможността за прищипване по улеите и върховете на резбата. Грешките при намаляване на външното измерение и увеличаване на вътрешния размер няма да повлияят на процеса на гримиране. Въпреки това, отклоненията в стъпката на резбата и ъгъла на профила ще доведат до задръстване на крепежния елемент.
Допустими отклонения на резбата
Толерантността и хлабината са най-често срещаните. При такива връзки номиналната стойност на средния диаметър е равна на най-голямата средна стойност на резбата на гайката. Отклоненията обикновено се броят от профилната линия, перпендикулярна на оста на резбата. Това се определя от GOST 16093-81. Допуските за диаметъра на резбата на гайките и болтовете се задават в зависимост от определената степен на точност (обозначена с число). Приетоследващата серия от стойности за този параметър: q1=4, 6, 8; d2=4, 6, 7, 8; D1=4, 6, 7, 8; D2=4, 5, 6, 7. За тях не са зададени отклонения. Поставянето на полетата за диаметър на резбата спрямо номиналната стойност на профила помага да се определят основните отклонения: горните за външните стойности на болтовете и долните за вътрешните стойности на гайките. Тези параметри директно зависят от точността и стъпката на свързване.
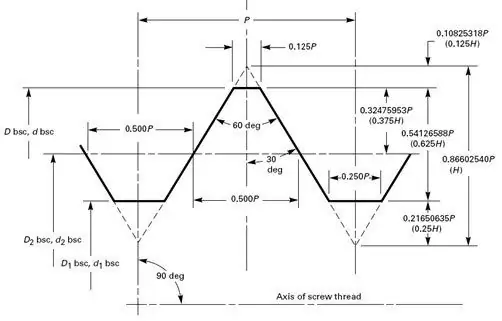
Допуски, прилягания и технически измервания
За производството и обработката на части и механизми с определени параметри, стругарът трябва да използва различни измервателни инструменти. Обикновено за груби измервания и проверка на размерите на продуктите се използват линийки, шублери и вътрешни габарити. За по-точни измервания - шублери, микрометри, габарити и т.н. Всеки знае какво е линийка, така че няма да се спираме на нея.
Дюблемерът е прост инструмент за измерване на външните размери на детайлите. Състои се от чифт въртящи се извити крака, фиксирани на една и съща ос. Има и пружинен тип шублер, той се настройва на необходимия размер с винт и гайка. Такъв инструмент е малко по-удобен от обикновен, тъй като запазва определената стойност.
Дюблемерът е проектиран да извършва вътрешни измервания. Има обикновен и пружинен тип. Устройството на този инструмент е подобно на шублер. Точността на инструмента е 0,25 мм.
Дюблемерът е по-прецизно устройство. Те могат да измерват както външни, така и вътрешни повърхности.обработени части. Стругарът, когато работи на струг, използва шублер за измерване на дълбочината на жлеба или перваза. Този измервателен инструмент се състои от вал с градуировки и челюсти и рамка с втори чифт челюсти. С помощта на винт рамката се фиксира върху пръта в необходимото положение. Точността на измерване е 0,02 мм.
Дълбокомер - това устройство е предназначено за измерване на дълбочината на канали и подрязвания. Освен това инструментът ви позволява да определите правилното положение на первазите по дължината на вала. Устройството на това устройство е подобно на шублер.
Микрометрите се използват за точно определяне на диаметъра, дебелината и дължината на детайла. Те дават показания с точност до 0,01 мм. Измерваният обект се намира между микрометърния винт и фиксираната пета, настройката се извършва чрез завъртане на барабана.
Вътрешните габарити се използват за точни измервания на вътрешните повърхности. Има фиксирани и плъзгащи се устройства. Тези инструменти са пръти с измервателни краища на топката. Разстоянието между тях съответства на диаметъра на определяния отвор. Границите на измерване за вътрешния габарит са 54-63 mm, с допълнителна глава, могат да се определят диаметри до 1500 mm.
Препоръчано:
Технологични процеси в машиностроенето. Автоматизирани системи за управление на процесите
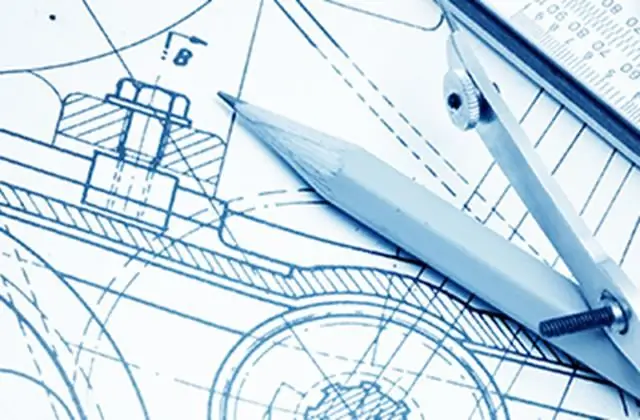
Технологичният процес е в основата на всяка производствена операция. Той включва набор от процедури, извършвани в определена последователност, чието действие е насочено към промяна на формата, размера и свойствата на произвеждания продукт. Основните примери за технологични процеси са механична, термична, компресионна обработка, както и сглобяване, опаковане, обработка под налягане и много други
Видове резби, използвани в машиностроенето
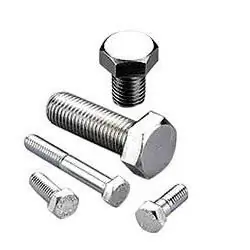
Нишката е богато украсена спирала с постоянна стъпка, приложена върху конична или цилиндрична повърхност. Това е основният елемент за свързване на два вида крепежни елементи. Към днешна дата за общи приложения в машиностроенето основните външни и вътрешни резби са метрични
Технология на машиностроенето: информация за специалността
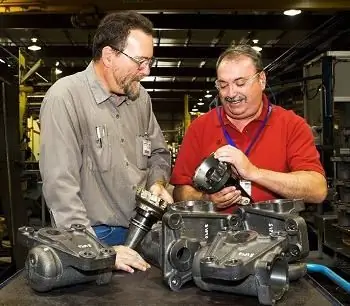
Инженерната технология е специалност, която остава в търсенето: всяка година поне 4 души кандидатстват за едно бюджетно място